
Evaluating the Application Feasibility of Lithium-Battery Electric Propulsion for Fishing Boats
This is an Open-Access article distributed under the terms of the Creative Commons Attribution Non-Commercial License(http://creativecommons.org/licenses/by-nc/3.0) which permits unrestricted non-commercial use, distribution, and reproduction in any medium, provided the original work is properly cited.
Abstract
Many small vessels such as fishing boats operate in the world's oceans; accordingly, interest in these small vessels’ exhaust-gas problem is increasing. Research on the application of electric-propulsion technology has been steadily conducted; however, the subject is limited to research ships or leisure boats, while research on application efficiency remains insufficient. This study attempts to apply lithium-battery electric-propulsion technology to small ships. A gross tonnage of 9.77, a representative fishing boat, is to be redesigned as a fully electrified ship. Without changing the main cabin’s dimensions and fuel tanks, the ship’s propulsion system is redesigned based on a lithium-battery electric-propulsion system. In addition, the redesigned system is compared with the original sample ship's diesel-propulsion system for application-effect analysis. The results indicate that under controlled sailing conditions, the weight and volume of the electric-propulsion system are 9.5 and 10.5 times those of the diesel-propulsion system, respectively. These values indicate that the system cannot meet fishing boats' high endurance requirements. Therefore, under the existing technical conditions, applying the full lithium-battery electric-propulsion system to solve the problem of high emissions from fishing boats shows limited feasibility.
Keywords:
Fishing boat, Ship design, Alternative energy, Electrification, Electric propulsion1. Introduction
The research project, “The State of World Fisheries and Aquaculture (SOFIA) 2022,” reported by the Food and Agriculture Organization of the United Nations, indicated that over 95% of the 4.1 million existing fishing fleet across the world are small-scaled vessels, with a maximum length of 24 m (FAO, 2022). Moreover, CO2 emissions due to global fisheries are increasing yearly (Greek et al., 2019); smaller vessels have higher carbon footprints than large-scale merchant vessels (Olmer et al., 2017).
Researchers have conducted studies focusing on fishing equipment, vessel types, hulls etc. to reduce the emissions of greenhouse gas from fishing vessels. Vessels using fishing lamps, combining light-emitting diode (LED) and metal halide (MH) lamps, or those replacing MH lamps with LED lamps can reduce fuel consumption during fishing and thus reduce CO2 emissions (An et al., 2013; An et al., 2017; An et al., 2014). Yu et al. (2021) and Tezdogan et al. (2018) examined the optimization of hulls, which has reduced the total ship resistance. Accordingly, fuel consumption and CO2 emissions have been reduced. Szelangiewicz et al. (2021) added bulbous bows to old fishing boats and achieved a reduction of 8.7% in CO2 emissions. In addition, owing to the unsatisfactory performances in CO2-emissions reduction through improving fishing equipment and optimizing the hulls, researchers believe that lightweight vessel hulls can provide better results. Such a method can reduce the overall ship resistance with a lighter weight of the entire vessel, thus alleviating the emissions problem. Li et al. (2018) have utilized the artificial bee-colony optimization algorithm to reduce the structural weight of the fishing boat made with fiberglass by 8.31%. Han et al. (2021) and Jeong et al. (2020) studied structural lightweight fiberglass fishing boats. The results showed that a reduction of 2.8% in the hull weight of fiberglass material could reduce CO2 emissions by 4.74%. By altering the ratio of the fiber to resin content (fiber content) in the fiberglass material, the material's specific strength can be improved, and the hull weight can be reduced by 27.00% while conforming to standard specifications (Han et al., 2021). However, none of these approaches can fundamentally solve fishing vessels’ emissions problems.
Greenhouse gas emissions mainly come from using fossil fuels (Olivier et al., 2005), while using replacements for fuels can fundamentally solve the emissions problems. The electric-propulsion system is entirely powered by batteries and has no emissions during sailing time. Therefore, it is believed that electric-propulsion ships will become the most applicable solution to reducing carbon emissions in the shipping industry (Wang et al., 2021). Compared with diesel-engine systems, applying electric-propulsion systems on ferries can reduce CO2 emissions by approximately 30% during the entire life cycle, considering the manufacture of batteries and grid-power generation (Wang et al., 2021). The case in Croatia has shown that, compared to diesel-propulsion systems, electric-propulsion systems can reduce CO2 and nitrogen oxide emissions by 64% and 99%, respectively, when applied to small-scaled inland ships (Perčić et al., 2021). The electric-propulsion system has been well applied to other types of ships. However, few examples of using electric-propulsion systems in fishing vessels have been reported.
This study attempted to analyze the performances of electric-propulsion systems when installed on fishing vessels owing to the high emissions from fishing vessels in coastal areas. Thus, the 9.77 ton fiberglass fishing boat built in South Korea was chosen as the object. An electric-propulsion system was designed considering the actual conditions, such as working time, sailing speed, and duration. The performances of the pure electric-propulsion system on the fishing boat were analyzed by comparing the total weight of the electric-power system with that of the diesel-engine propulsion system.
2. Research methods
To evaluate the feasibility of using an electric-propulsion system to solve fishing vessels’ emissions problems, the representative Korean fiberglass fishing boat equipped with a diesel engine with a gross tonnage of 9.77 was chosen as the research object. First, without altering the main engine room and fuel tanking, the sample ship was redesigned with an electric-propulsion system, including selecting the motor and lithium-ion (Li-on) batteries, estimating total energy consumption, and calculating the total weight of the batteries. Next, the electric-propulsion system was compared to the original diesel-engine propulsion system in terms of energy consumption. This study did not change the fish cabin or the boat structure, except the propulsion system, for consistency.
To properly redesign the fishing boat’s propulsion system, it is necessary to set the actual navigation conditions, such as duration and speed. This study defined the sailing scenarios, considering this type of fishing vessel’s actual situation: sailing 5 days a week and 8 h a day. On the departure voyage toward the fishery, the sailing speed was 12 knots, lasting 1 h and 28 min. When working at the fishery, the engine load was 30%, lasting 4 h. On the return voyage from the fishery, the sailing speed was 7 knots, lasting 2 h and 32 min.
3. Selection and analysis of the sample ship
3.1 Introduction to the sample ship
A representative fiberglass fishing boat from South Korea, with a length of 19.1 m, a displacement tonnage of 42, and a gross tonnage of 9.77, was selected as the sample ship, which was designed by the Research Institute of Medium & Small Shipbuilding (South Korea). The sample ship’s design drawing and major parameters are shown in Fig. 2 and Table 1, respectively. The Volvo Penta D16-750, with a weight of 1750 kg and a volume of 3275.1 L, was chosen as the inboard diesel engine. The MG-5145, with a weight of 325 kg and volume of 193 L, was used as the marine transmission system. Their specifications are listed in Table 2.
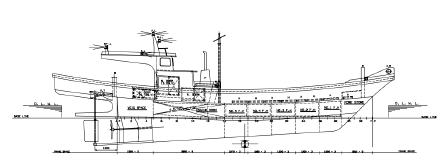
Design drawing of the GT 9.77-ton fishing boat (Research Institute of Medium & Small Shipbuilding, 2006)
3.2 Estimation of diesel consumption
Fuel is indispensable to the propulsion system. As mentioned above, a comparison with the diesel-engine propulsion system was performed to verify the performance of the Li-on battery electric-propulsion system. Consequently, the diesel consumption must be quantified, which was done considering different sailing speeds.
From the parameters of the sample ship, when sailing at its maximum speed of 12 knots, the Froude Number () is 0.53. Therefore, categorized by the navigation type, the sample ship belongs to the Semi-planing group (Molland et al., 2017). To correctly estimate its resistance, the commonly used estimation methods for this type of ship are Holtrop, Van Oortmerssen, and Compton methods (Santosa et al., 2022; Pahlawan et al., 2020; Puspita et al., 2022; Romadhoni, 2020; Xhaferaj, 2022; Prananda et al., 2020; Yasim et al., 2021). All three methods mentioned above were adopted in this study, with the help of the sample ship’s three-dimensional digital model and the Maxsurf Resistance module, to improve the accuracy of the resistance-estimation results. The estimation results are shown in Fig. 3.
From Fig. 3(a), the fitting result of the resistance at 12 knots (the maximum speed) is 57.10 kN, and the effective horsepower is 472.30 hp. In the real scenario, the ship will be affected by the ocean’s winds and waves. Hence, it is usually necessary to consider sea margin when estimating the main engine’s power requirement. Similarly, the engine margin should also be involved, which considers the aging of machinery and safety of sailing in inclement weather conditions. Fig. 3(b) shows a plot of the effective horsepower curve based on the fitting result. Considering the 15% sea margin and 10% engine margin, the Maximum Continuous Rating (MCR) required for the maximum speed of 12 knots is 603 hp.
To estimate the diesel consumption under the scenario predefined in the research methods section, the diesel engine’s horsepower and corresponding fuel consumption curves under different operating conditions (rotational and speed) are required. Consequently, the Volvo D16-750 diesel engine’s technical data (Volvo Penta, 2016) are used for the estimation, as shown in Fig. 4.
According to the predefined scenario, the sample ship’s main engine has three operating states, as shown in Fig. 4 (a). During the departure voyage, the diesel engine’s required power is 603 hp, and the Rotation Per Minute (RPM) is approximately 1,800. The required power during the return voyage is 40 hp, and the RPM is approximately 760. When the engine load is 30%, the diesel engine’s required power is 218 hp, and the RPM is approximately 1,280. As shown in Fig. 4(b), the main engine’s fuel-consumption curve shows that the specific diesel consumption is approximately 7.1 L/h for an RPM of 760, approximately 35.7 L/h for an RPM of 1,280, and 107.5 L/h for an RPM of 1,800. Combined with the scenario, the daily and weekly diesel consumptions are 318.4 L and 1592.0 L, respectively (as shown in Table 3).
The diesel has a density of 0.84 kg/L (SUH et al., 2010). Accordingly, the weekly consumption of diesel would weigh approximately 1337.28 kg. The fuel tank has dimensions of 1000 × 4000 × 400 mm and a weight of 305.7 kg. Therefore, for one-week sailing, the weight of the diesel-engine propulsion system accounts for 3717.98 kg, and the required volume is 5068.10 L, as shown in Table 4.
4. Design of the Li-on battery-propulsion system for the fishing boat
To verify the applicability of pure Li-on battery-propulsion systems to fishing vessels, the design of such a system is presented in this section and compared with the sample ship’s in the next section to analyze the performance of retrofitting conventional fishing boats with pure electric-propulsion systems.
4.1 Design flow of the Li-on battery-propulsion system
When designing the propulsion system, selecting the motor and battery unit is essential because the battery units will form a Li-on cartridge-battery system to supply the electric motor. Similar to the design flow of a diesel-propulsion system, the design of a marine Li-on battery-propulsion system must estimate the power consumption under the predefined scenario and corresponding weight of the cartridge-battery system. Generally, it can be partitioned into four steps, as shown in Fig. 5.
The first step is determining the sailing speed and duration according to the ship’s information and scenario. The ship’s information and scenario were introduced in the previous section and are not repeated here. The second step is to determine the ship’s resistance according to its dimension and select the motor and Li-on cartridge-battery system (comprising a series and parallel battery unit). The third step is to estimate the power consumption. First, based on the different current requirements at different sailing speeds and voltage level of the power supply of the cartridge-battery system, the power consumption against sailing speed can be estimated. Next, the total power demand is determined according to the sailing duration. Finally, considering the power capacity of an individual Li-on battery unit and total power demand, the number of battery units and total weight of the cartridge-battery system under the predefined scenario can be calculated.
4.2 Selection of the electric motor and cartridge-battery system
As mentioned earlier, the diesel engine used in the sample ship is a Volvo D16-750. When sailing at the maximum speed of 12 knots, the MCR of the main engine is 603 hp. When selecting the motor, it is assumed that the diesel-engine and electric-propulsion systems share the same propeller efficiency.
This study selected two LGM i-330 motors (DC motor). Each has a power of 330 hp, weighs 437 kg, and has a volume of 793.4 L (Oh et al., 2018). Owing to the diesel engine's mechanical structure, the torque varies with speed. However, the same torque will be produced with an electric motor regardless of the speed. Therefore, this study did not include the transmission system in the electric-propulsion system.
The selected battery unit is the BF 86; the cartridge-battery system is the BF 86 made with Li-on battery, with a rated voltage of 86.4 V, a capacity of 14.52 kWh, a weight of 80 kg, and a volume of 120 L (Electrine), as shown in Tables 5 and 6. According to the operating voltage range of the LGM i-330 motor (LG Marines, 2017) and the specification of the Li-on battery-unit BF 86, eight battery units were connected in series to form a Li-on cartridge-battery system. The resulting voltage is 691.2 V, capacity is 116.16 kWh, weight is 640 kg, and volume is 960 L.
4.3 Estimation of electric-power consumption and requirements on Li-on cartridge-battery system
Like the diesel-engine propulsion system, the Li-on battery-propulsion system has different power-consumption levels under different scenarios. Therefore, it is important to consider the difference in sailing speed when estimating power consumption. Hence, plotting current values against sailing speed is indispensable. Here, the technical data provided by LGM is utilized, as shown in Fig. 7. Similar to the diesel-propulsion system analysis and based on the assumptions made above, three of the sample ship's operating states are considered: 7 knots, 12 knots, and 30% engine load. As plotted in Fig. 7, the required current for the departure and return voyages are 244.07 A at 12 knots and 228.49 A at 7 knots, respectively. The voltage of the Li-on cartridge-battery system is 691.2 V. According to Equation 1, the power consumption per unit time is 168.70 kWh during the departure voyage at 12 knots and 157.93 kWh during the return voyage at 7 knots. When sailing at the 30% engine-load state, the power is 198 hp (147.65 kW), and the power consumption per hour is 147.65 kWh. According to Equation 2, the daily power consumption is 1238.1 kWh, and the total weekly power consumption is 6190.5 kWh (as shown in Table 6).
where U denotes the voltage, whose unit is V; I denotes current, whose unit is A; t denotes time, whose unit is h.
where Wi, (i = 1,2,3) denotes the daily power consumption during the departure, fishing, and return voyage.
Each Li-on cartridge-battery system has a capacity of 116.16 kWh and requires 6190.5 kWh of energy weekly. Considering the scenario mentioned above, a 54 Li-on cartridge-battery system was desirable. As mentioned earlier, each cartridge-battery pack weighs 640 kg and has a volume of 960 L. Consequently, for one-week sailing, the required Li-on cartridge-battery pack weighs 34560 kg and has a volume of 51840 L. Considering the requirements of the electric motor for one-week sailing, the weight and volume of the electric propulsion system are 35434 kg and 53426.8 L, respectively (as shown in Table 7).
5. Performance analysis of the fishing boat with electric-propulsion system
5.1 Performance of the fishing boat with electric-propulsion system under the predefined scenario
To determine the applicability of the electric-propulsion system to fishing boats, both the restoration of the diesel-engine propulsion system and the design of the electric-propulsion system were performed on the fishing boat of 9.77 gross tonnage. In the one-week sailing scenario, the weights and volumes of the diesel-engine and electric-propulsion systems are shown in Tables 4 and 8.
Fig. 8 shows that in the one-week sailing scenario, the weight of the electric-propulsion system is 9.5 times that of the diesel-engine propulsion system, and the volume required by the electric-propulsion system is 10.5 times that of the diesel-engine propulsion system. Tables 4 and 6 indicate that the inherent weight of the diesel-engine system (namely, the sum of the weights of the diesel propeller, fuel tank, and transmission system) is twice that of the electric-propulsion system (namely, the weights of the motor and propeller). Nevertheless, the final weight and volume are 9.5 and 10.5 times greater, respectively. This result is because the battery’s weight and volume are more significant than those of the diesel and fuel tanks. In addition, the main application of a fishing boat is to fish, which makes its volume a dominant factor over its weight. Accordingly, the fishing boat’s owner will not allow the space of the fish cabin to be occupied. In summary, the electric-propulsion system is unacceptable to fishing boat owners.
5.2 Impact of sailing range on the weight of Li-on battery-propulsion system
In the previous section, it was concluded that pure Li-on battery-propulsion systems had low feasibility. However, because the diesel engine weighs much more than the electric motor, within a certain range, the electric-propulsion system outperforms the diesel-engine propulsion system. Thus, this section analyzes the correlation between battery capacity (measured in nautical miles, NM) and system weight when sailing at 7 and 12 knots, respectively, as shown in Fig. 9.
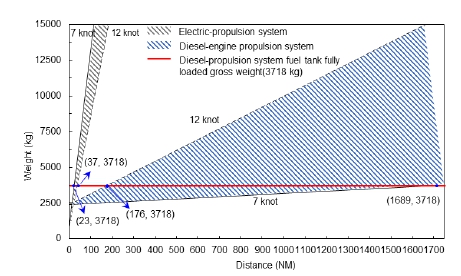
Variation of the total weight of propulsion system against the sailing range (comparison between diesel-engine and electric-propulsion systems)
If the diesel-engine propulsion system is to be converted into an electric-propulsion system, the variable part of the weight is that of the diesel-propulsion system when the fuel tank is fully loaded. The sample ship's fuel tank has a volume of 1600 L. The total weight of the entire diesel system is 3718 kg (marked with the red line in Fig. 9) when the tank is full. Fig. 9 shows that the electric-propulsion system has more significant changes in weight against the unit sailing range than the diesel-engine propulsion system. This is because the energy-storage density of the Li-on battery is much lower than that of diesel. Thus, when sailing at 7 knots, the weight of the electric-propulsion system is limited to 3718 kg while the range is only 23 NM. However, the diesel-engine propulsion system has a range of 1689 NM when sailing at 7 knots. At 12 knots, the electric-propulsion system’s range reaches 37 NM, which is higher than that for 7 knots, while that of the diesel-engine propulsion system decreases to 176 NM.
From the above analysis, it can be concluded that the electric-propulsion system outperforms the diesel-engine propulsion system when shorter ranges are involved. Such a result is consistent with the facts about the electric-propulsion vessels in service. The electric vessels in service, such as Norway’s Ampere ferry, Germany’s Sankta Maria II ferry, Finland’s Q30 yacht, and China’s Junlv yacht (Xinhua, 2020), are characterized by a short distance and time for a single voyage, as listed in Table 8. In contrast, fishing boats generally require a longer time to fish and will sail a longer distance. Therefore, the full electric-propulsion system is unsuitable for fishing vessels with longer-range requirements.
5.3 Impact of sailing speed on the weight of Li-on battery-propulsion system
In the previous section, the performance of the electric-propulsion system is better than that of the diesel-engine propulsion system when shorter ranges are involved. However, it can be concluded from Fig. 9 that the ranges for the diesel-engine and electric-propulsion systems have opposite reactions to a change in speed (at both 7 knots and 12 knots). For the electric-propulsion system, with the same range, the system weighs more when sailing at 7 knots than at 12 knots. However, the opposite result is obtained for diesel-engine propulsion systems.
This section analyzes the correlation between sailing speed and system weight. First, the sailing range is defined. As mentioned earlier, the sailing distance (round trips for five days) is 177 NM. Diesel fuel or electricity consumption during its working time will slightly affect the sailing range. Hence, the consumed quantity of either fuel or electricity is neglected. Therefore, with a range of 177 NM, the variations of sailing speed against the system weight are shown in Fig. 10.
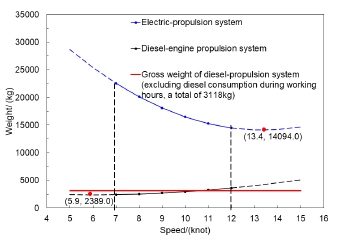
Variations of system weight against sailing speed with identical range (comparison between diesel-engine and electric-propulsion systems)
Fig. 10 shows an apparent difference in sailing speed when the sample ship bears a minimum total weight of different propulsion systems. For the electric-propulsion system, the speed for the minimum system weight is approximately 13.4 knots; for the diesel-propulsion system, it is approximately 5.9 knots. Consequently, when considering the weight of the propulsion system, the diesel-engine propulsion system performs better at a lower speed than at a higher speed, which is the opposite for the electric-propulsion system. In addition, when only the consumption of diesel or electricity during the round trip is considered, the weight of the diesel-propulsion system is 3118 kg (marked with the red line in Fig. 10). This is presented in Tables 6 and 7 above. Therefore, even at its lowest speed, the electric-propulsion system still cannot meet the weight requirements for the sample ship with the diesel-engine propulsion system.
6. Conclusion
This study was based on the representative Korean fishing boat with a gross tonnage of 9.77. Through the design of an electric-propulsion system and comparative analyses with the diesel-engine propulsion system, the performances of the electric fishing boat were evaluated. The conclusions are as follows:
Assuming one week’s actual sailing, the weight and volume of the electric motor are smaller than those of the diesel engine. Thus, the total weight of the electric-propulsion system is much greater than that of the diesel-engine propulsion system (9.5 times) while it occupies much more space than the diesel-engine propulsion system does (10.5 times). This is because the desired quantity of Li-on battery is much larger than that of diesel fuel to meet the predefined sailing scenario. For vessels such as fishing boats, the space of fish compartments is crucial, which cannot be given away for storing Li-on batteries, despite being indispensable to the sailing scenario.
In short, current Li-on-battery technology has been found to be inefficient when used for long endurance working, such as fishing boats, even for small vessels. To solve the current limitations, battery technology with improved efficiency is essential. To solve the problem of emissions from fishing vessels, it is more advisable to seek solutions based on a hybrid diesel-fuel and Li-on-battery propulsion system. Another solution entails replacing diesel with lower-emission fuels, such as Liquefied Natural Gas (LNG), biofuel, and methanol. In addition, for actual construction, the acts and standards for fishing boats and electric-propulsion ships must be considered to ensure safety.
Acknowledgments
This research was financially support by Jeollannam-do “2023 R&D supporting program” operated by Jeonnam Technopark and grant from the National R&D Project of “Demonstration of power generation system and RCI technology using ship waste heat(2/6)” funded by the Ministry of Oceans and Fisheries, Korea.
References
-
An, H.C., Bae, J.H., Bae, B.S. and Park, J.M., 2013. Operating performance of squid jigging vessel using the LED and metal halide fishing lamp combination. Journal of the Korean Society of Fisheries and Ocean Technology, 49(4), pp.395-403.
[https://doi.org/10.3796/KSFT.2013.49.4.395]
-
An, Y.I., 2014. Fishing efficiency of high capacity (360W) LED fishing lamp for squid Todarodes pacificus. Journal of the Korean Society of Fisheries and Ocean Technology, 50(3), pp.326-333.
[https://doi.org/10.3796/KSFT.2014.50.3.326]
-
An, Y.I., He, P., Arimoto, T. and Jang, U.J., 2017. Catch performance and fuel consumption of LED fishing lamps in the Korea hairtail angling fishery. Fisheries Science, 83(3), pp.343–352.
[https://doi.org/10.1007/s12562-017-1072-6]
- Electrine. Battery series. [Online] Available at: http://www.electrine.co.kr/products/battery, [Accessed 19 March 2023].
- FAO., 2022. The state of world fisheries and aquaculture 2022. Towards Blue Transformation. FAO Rome.
-
Greer, K., Zeller, D., Woroniak, J., Coulter, A., Winchester, M., Palomares, M.D. and Pauly, D., 2019. Global trends in carbon dioxide (CO2) emissions from fuel combustion in marine fisheries from 1950 to 2016. Marine Policy, 107: 103382.
[https://doi.org/10.1016/j.marpol.2018.12.001]
- Han, Z.-Q., Jang. J., Lee. K. and Oh. D., 2021. Lightweight-laminate design of fishing boat considering mechanical properties of glass fiber reinforced polymer. Ship Building of China, 62(02), pp.132–144.
-
Jeong, S., Woo, J.H. and Oh, D., 2020. Simulation of greenhouse gas emissions of small ships considering operating conditions for environmental performance evaluation. International Journal of Naval Architecture and Ocean Engineering, 12, pp.636–643.
[https://doi.org/10.1016/j.ijnaoe.2020.07.006]
- LG Marines. 2017. I-330. [Online] Available at: https://company.metstrade.com/Image/Download?docid=75939&dl=MIJNRAI_TOP_LIBRARY<c=MIJNRAI_LOGIN_PRIVATEFILE, [Accessed 24 March 2023].
-
Li, K., Yu, Y., Wang, Y. and Hu, Z., 2018. Research on structural optimization method of FRP fishing vessel based on artificial bee colony algorithm. Advances in Engineering Software, 121, pp.250-261.
[https://doi.org/10.1016/j.advengsoft.2018.03.011]
- Marind. 2006. MG-5154. [Online] Available at: https://www.pjpower.com/products/twindisc/marine-transmissions/mg-5145, [Accessed 19 March 2023].
-
Molland, A., Turnock, S. and Hudson, D., 2017. Hull form design. In ship resistance and propulsion: practical estimation of ship propulsive power. Cambridge: Cambridge University Press.
[https://doi.org/10.1017/9781316494196]
-
Oh, D., Jung, S. and Jeong, S., 2018. Effect of a lightweight hull material and an electric propulsion system on weight reduction: Application to a 45ft CFRP electric yacht. Journal of The Korean Society of Marine Environment & Safety, 24(6), pp.818–824.
[https://doi.org/10.7837/kosomes.2018.24.6.818]
-
Olivier, J.G., Van Aardenne, J.A., Dentener, F.J., Pagliari, V., Ganzeveld, L.N. and Peters, J.A., 2005. Recent trends in global greenhouse gas emissions: regional trends 1970–2000 and spatial distribution of key sources in 2000. Environmental Sciences, 2(2-3), pp.81–99.
[https://doi.org/10.1080/15693430500400345]
- Olmer, N., Comer, B., Roy, B., Mao, X. and Rutherford, D., 2017. Greenhouse gas emissions from global shipping, 2013–2015 Detailed Methodology. International Council on Clean Transportation: Washington, DC, USA.
- Pahlawan, M.R., Kadhafi, M., Sunardi, S. and Yulianto, E. S., 2020. Analysis of existing traditional fishing vessel with hold compartment for live fish. International Conference on Fisheries and Marine Research, 1(1), pp 75–78.
-
Perčić, M., Vladimir, N. and Koričan, M., 2021. Electrification of inland waterway ships considering power system lifetime emissions and costs. Energies, 14(21): 7046.
[https://doi.org/10.3390/en14217046]
-
Prananda, J., Koenhardono, E.S. and Tjoa R.C., 2020. Design of an optimum battery electric fishing vessel for Natuna sea. International Journal of Marine Engineering Innovation and Research, 4(2), pp.104-114.
[https://doi.org/10.12962/j25481479.v4i2.3455]
-
Puspita, H.I.D., Kusnadi, R.F. and Syaikhu, D., 2022. Optimalisasi lambung kapal penangkap ikan dengan bahan dasar fiberglass di pelabuhan perikanan puger. Zona Laut: Journal of Ocean Science and Technology Innovation, 3(1). pp.38–46.
[https://doi.org/10.20956/zl.v3i1.11087]
- Q-yacht. Q30 – Experience the Electric Silence. [Online] Available at: https://q-yachts.com/q30/, [Accessed 19 March 2023].
- Research Institute of Medium & Small Shipbuilding. 2006. Design drawings of GT 9.77-ton fishing boat.
- Romadhoni, R. 2020. Spesifikasi teknis pembangunan kapal ikan kapasitas 3 gross tonage berbahan fiberglass. Seminar Nasional Industri dan Teknologi, 97–107.
-
Santosa, A.W.B., Mausulunnaji, M.F., Setiyobudi, N., Chrismianto, D. and Hadi, E.S., 2022. Engine propeller matching analysis on fishing vessel using inboard engine. Journal of Applied Engineering Science, 20(2), pp.477–484.
[https://doi.org/10.5937/jaes0-31979]
- Ship Technology. 2015. Ampere Electric-Powered Ferry. [Online] Available at: https://www.ship-technology.com/projects/norled-zerocat-electric-powered-ferry/, [Accessed 19 March 2023].
-
Suh, J,. Wang, W. and Kim, S., 2010. An experimental study on characteristics of exhaust emissions with fuel properties changes in a diesel engine for small-sized fishing vessel. Journal of the Korean Society of Fisheries and Ocean Technology, 46(4), pp.487–494.
[https://doi.org/10.3796/KSFT.2010.46.4.487]
-
Szelangiewicz, T., Abramowski, T., Żelazny, K. and Sugalski, K., 2021. Reduction of resistance, fuel consumption and GHG emission of a small fishing vessel by adding a bulbous bow. Energies, 14(7), 1837.
[https://doi.org/10.3390/en14071837]
-
Tezdogan, T., Shenglong, Z., Demirel, Y K., Liu, W., Leping, X., Yuyang, L. and Incecik, A., 2018. An investigation into fishing boat optimization using a hybrid algorithm. Ocean Engineering, 167, pp.204-220.
[https://doi.org/10.1016/j.oceaneng.2018.08.059]
- Visitmosel. “Sankta Maria II. [Online] Available at: https://www.visitmosel.de/poi/faehre-sankta-maria-ii, [Accessed 19 March 2023].
- Volvo, P. 2016. D16-750. [Online] Available at: https://www.haismascheepsmotoren.nl/wp-content/uploads/2019/02/Product-leaflet-D16-MH.pdf, [Accessed 19 March 2023].
-
Wang, H., Boulougouris, E., Theotokatos, G., Zhou, P., Priftis, A. and Shi, G., 2021. Life cycle analysis and cost assessment of a battery powered ferry. Ocean Engineering, 241, 110029.
[https://doi.org/10.1016/j.oceaneng.2021.110029]
-
Xhaferaj, B. 2022. Investigation on some conventional hulls forms of the predictive accuracy of a parametric software for preliminary predictions of resistance and power. Brodogradnja: Teorija i praksa brodogradnje i pomorske tehnike, 73(1), pp.1–22.
[https://doi.org/10.21278/brod73101]
- Xinhuanet. 2020. The full electric cruise ship “Junlv” made its maiden voyage in Wuhan. [Online] Available at: http://m.xinhuanet.com/hb/2020-06/24/c_1126152950.htm, [Accessed 19 March 2023].
-
Yasim, A.Y.A., Wibowo, R.K.K. and Priohutomo, K., 2021. Study of main engine and propeller matching on fishing vessel after reparation (case study of KM. Km. Nelayan 2017–572). Wave: Journal of Maritime Technology, 15(1), pp.11–20.
[https://doi.org/10.29122/jurnalwave.v15i1.4724]
-
Yu, J.W., Lee, M.K., Kim, Y.I., Suh, S.B. and Lee, I., 2021. An optimization study on the hull form and stern appendage for improving resistance performance of a coastal fishing vessel. Applied Sciences, 11(13), 6124.
[https://doi.org/10.3390/app11136124]