
고주파 유도가열을 이용한 오목 곡면 곡가공에 관한 연구
Abstract
In shipbuilding, accurate fabrication of curved hull plates is one of the most important steps, since the shape of ship hull, which is very critical in the overall performance of a ship, is a collection of such plates. The curved hull plates forming process requires a significant amount of time by skilled workers in shipbuilding. In general, the workers cause thermal distortion in the plate and forming initial shape using gas heat source. So shipbuilding companies need skilled workers who have long experience. To solve the problem, a lot of researchers tried to develop automation system for curved hull plates. In this paper, we propose automatic heating system with gantry robot, high frequency induction heater to replace the gas heat source and automatic measurement system. We apply the system to forming concave type plate that is actually used in ship manufacturing. In addition, a system was developed to automatically generate heating information, such as the heating location and the heating speed, for actual heating process. Then the system was applied to the actual heating material. It is shown that the proposed triangle heating pattern makes desired concave shape successfully. The induction heating system showed that it can be used for automation system of curved hull plates forming process replacing gas heat source.
Keywords:
Concave type, Triangle heating, Hull forming, Induction heating, Automatic heating키워드:
오목형, 삼각가열, 곡가공, 유도가열, 자동 가열1. 서론
선체 곡면을 제작하는 방법에는 크게 롤벤딩이나 프레스와 같은 기계로 힘을 가하는 냉간 가공 하는 방법과 선상가열 및 삼각가열로 곡면의 특정 부분을 가열하여 수축 및 굽힘을 유발하는 방법이 있다. 생산성 향상이 중요한 조선업에서 전체 부재의 약 70% 이상을 차지하는 곡면 부재에 대해 작업자 경험에 의한 수작업으로 진행되고 있는 선상가열 및 삼각가열의 자동화는 가공 단계의 병목 과정을 해소해주어 생산성을 높이는데 도움이 된다고 할 수 있다. 선상가열 및 삼각가열 자동화는 두 가지 단계로 나누어 진행된다. 첫 번째는 가열 조건에 따른 변형을 예측하는 부분이고, 두 번째는 정확한 변형 해석에 의한 잔류변형 예측이 가능하다는 전제하에 가열 위치 및 형상 등의 가열 정보를 결정하는 부분이다.
선상가열 및 삼각가열에 의한 판의 변형을 예측하는 방법은 크게 열탄소성 해석법과 고유변형도법 두 가지로 나뉘어진다. 열탄소성 해석법은 열량 및 열량의 투입 방법을 입력 값으로 하여 가열시 발생하는 열전도에 따르는 탄소성 반복 과정을 역학적으로 추적하는 방법이다. 입열원은 주로 가스나 고주파 유도가열 장비를 사용하는데 가스에 비해 고주파 유도가열 장비가 소음이 적고 입열량을 정확히 예측할 수 있다는 장점이 있기 때문에 자동화에는 가스 가열보다는 고주파 유도가열이 적합하다고 할 수 있다. Ueda et al.(1994)과 Kang et al.(2000), Kim(2002)은 고주파 유도가열을 이용한 선상가열에서 강판의 열탄소성 변형에 관한 실험적 해석 및 수치적 해석에 관한 연구를 수행하였다. Terasaki et al.(2003)은 가스 열원으로 수행하는 삼각가열에 대하여 가스 토치의 이동속도, 높이를 조절하여 삼각가열에 대한 열탄소성 해석을 수행하였다. 고유변형도(inherent strain)법은 재료에 존재하는 비탄성 변형도를 이용하여 변형을 예측하는 방법이다. Jang et al.(2001a, 2001b, 2003)은 상변태 과정을 고려한 고유변형도를 등가하중법에 반영시켜 선상가열 변형해석을 수행하였다. Seo(2000)은 가스 열원을 사용한 삼각가열에 대하여 가열 면적과 가열 시간이 선형적으로 길어지는 모델을 가정하여 고유변형도 영역을 타원으로 가정하고 해석을 수행하여 잔류 변형량을 구하였다. 또한, 삼각가열에서 선형성이 성립함을 밝혀냈다. Kim(2001)은 삼각가열에 대해 고유변형도법을 이용하여 고유변형도에 의한 등가하중을 구하여 간이 해석법을 제안하였다. 고유변형도를 이용한 등가하중법은 탄성 해석을 수행하므로 간편하게 결과를 얻을 수 있는 반면, 적절한 고유변형도의 가정이 어렵고 응력을 계산할 수 없다는 단점이 있다.
변형을 이론적으로 해석할 수 있는 기반이 생기면 선상가열과 삼각가열의 경우 가열 위치 및 형상 등의 가열 정보를 결정할 수 있어야 한다. 선상가열의 가열선 결정에 대해서는 Ueda et al.(1994)이 고유변형도를 집중 분포시킬 판 위의 위치 즉, 가열선의 경로를 판의 3차원 유한요소해석 결과로 변형도의 크기가 주위보다 큰 몇 요소를 택함으로써 선정하고 있고, 그것이 실제 작업 내용과 유사하다는 것을 보이고 있다. 하지만, 한 부재에 대한 선상가열 정보를 얻기 위해 여러 번의 3차원 탄성 대변형 해석과 파라메트릭 연구(parametric study)를 수행해야 하므로 방대한 계산 시간이 필요하다. Ryu(2002)는 가열선에 수직으로 주요 굽힘과 수축이 발생하는 선상가열 및 삼각가열 현상에 착안하여 판의 변형기하해석을 통해 주 변형률(principal strain)의 방향을 구하고 이를 가열선 결정에 이용하였다.
위와 같이 현재까지의 관련 연구 동향을 살펴보면 선상가열과 삼각가열에 대한 선행 연구들은 가열 조건에 따른 변형을 예측하는 부분에 그 중점을 두었으며 가열 정보 결정 부분에 대해서는 선상가열에 대해서만 연구가 진행되어왔을 뿐 삼각가열에 대해서는 연구가 전무한 실정이다.
조선업의 곡가공 분야 중 비교적 연구가 활발히 수행되어 온 선상가열 보다는 상대적으로 연구가 미비한 삼각가열에 대해 가열 형상 및 위치를 결정하는 방법을 제시하고자 한다. 이는 조선업계의 난제 중 하나로 손꼽히는 곡가공 자동화 해결을 위해 수행되어야 할 연구이며, 연구가 전무한 삼각가열 형상 및 위치 결정에 관해 후행 연구의 초석이 될 수 있다는데 의의가 있다.
본 연구에서는 고주파 유도가열 열원에 의한 변형특성과 Shin et al.(2003), Ko et al.(2005), Park et al.(2007)이 제안하는 가공정보 생성 알고리즘을 결합하는 통합 가공정보 생성 시스템을 개발하였다. 개발된 가열정보 생성시스템과 고주파 유도가열 장치를 활용하여 삼각가열만으로도 곡가공이 가능한 오목형(concave)형 곡면 성형에 대하여 자동 열간가공을 하였고, 그 결과를 비교 평가 하였다.
2. 가열정보 생성 알고리즘
곡면가공은 냉간가공(프레스 벤딩) 후에 열을 가하여 철판에 소성변형을 일으켜 최종 목적형상을 제작하는 방법을 사용한다. 이때 가열할 위치 정보 및 가열 패턴 등에 대한 정보를 제공하여야 한다. 본 연구에서는 Kim(2007, 2009)이 제안한 가열정보 이론에 근거하여 가열위치와 가열세기를 결정하였다. 그 과정은 다음과 같이 두 단계로 진행된다.
∙ 단계 1: 삼각가열의 개수 및 위치 결정은, 종방향 변에 대한 하나의 각변형량으로 끝단의 곡량을 맞추기 위해, 종방향 각 변에서의 면내 변형률 분포의 평균을 계산하고 그 변을 대표하는 하나의 면내 변형률 분포 형태를 가정하여 구한다(Fig. 1). 이때 면내 변형률은 계산은 Ryu(2002)의 최소 변형률 에너지를 갖도록 판을 전개하는 변형이론과 알고리즘을 적용하였다.
∙ 단계 2: 단계 1에서 구한 종방향 변의 평균 면내 변형률 분포로 실제 삼각가열 형상의 크기를 결정한다. 면내변형률 계산 과정에는 실제 가열 과정에서 발생 가능한 판의 내부와 외부의 강성차이 등에 의한 수축 편차는 반영되어 있지 않으며, 계산된 면내 변형률의 분포 또한 넓고 다양하게 분포되는 단점이 있어, 평균 면내변형률 분포형태를 가정한 삼각가열 형상이 계산되도록 하였다. 사다리꼴 모양의 삼각가열 형상 윗변의 길이를 사용될 열원의 직경을 고려하여 60mm로 고정하고, 계산된 면내 변형률 값이 60mm이 되기 위한 스케일 팩터(scale factor) K를 정의하여 결정하고, 아랫변의 면내 변형률 값에 K를 곱하여 아랫변의 길이를 계산한다(Fig. 2).
삼각가열의 높이는 계산된 평균 면내 변형률 분포 높이를 그대로 사용한다.
사용된 열원에 대한 변형량 정보는 자동화 가열장치의 열원으로 사용된 고주파 유도가열 열원에 대해서 가열실험과 유한요소법을 통하여 수식으로 도출하였다. 유도가열은 전자기적인 현상과 열(熱)적인 현상을 동시에 일으키게 된다. 따라서 유도가열 열원에 의한 유한요소 해석은 가열 속도, 전류. 주파수 등을 입력 파레메터로 하여 전자기장 해석과 온도 해석을 순차적으로 반복하여 계산하여 나온 결과이다 (Bae et al. (2007)).
조선용 후판 강재에 대하여 고주파 유도가열 실험과 유한요소 해석을 통하여 나온 결과가 Fig. 3의 입열량-수축변형 관계를 도출하였다.
3. 삼각가열 가열패턴 생성 알고리즘
열원 중심이 이동할 좌표를 계산하는 단계에 있어서, 먼저, 결정된 가열위치 및 삼각형상에 따라 삼각형의 세 꼭지점에 X,Y,Z의 좌표값이 가열선 생성 시스템에서 제공된다(Fig. 4).
각 꼭지점간 선분의 중점(Xa,Ya,Za)~(Xc,Yc,Zc)을 계산하고(Fig. 5), Fig. 6에 도시된 바와 같이, 각 꼭지점과 대응되는 변에 생성된 중점을 잇는 선분을 1 : (N-1) 등분하는 내분점(X1c,Y1c,Z1c)~(X3a,Y3a,Z3a)을 계산하여, 내부에 새로운 삼각형 형상을 구성한다. 이때, N의 값은 꼭지점과 중점의 거리를 EL(EL effective length : 가공에 사용될 열원의 유효거리 또는 열원의 반경)로 나눈 몫이며, EL은 열원에 따라 적절히 조절된다. 다음으로, 새롭게 계산된 내분점(X1c,Y1c,Z1c)~(X3a,Y3a,Z3a)을 이용하여, (X1c,Y1c,Z1c)~(X2b,Y2b,Z2b)사이의 N1과, (X1c,Y1c,Z1c)~(X3a,Y3a,Z3a)사이의 N2, (X2b,Y2b,Z2b)~ (X3a,Y3a,Z3a)사이의 N3를 계산한다 (Fig. 7). 이때 N1~N3는 각 꼭지점간 거리를 EL로 나눈 몫이다. 그리고, N1과 N2중에서 큰 값으로 (X1c,Y1c,Z1c)~(X2b,Y2b,Z2b)와 (X1c,Y1c,Z1c)~(X3a,Y3a,Z3a)를 N등분하고, (X2b,Y2b,Z2b)~(X3a,Y3a,Z3a)는 N3로 N등분한다.
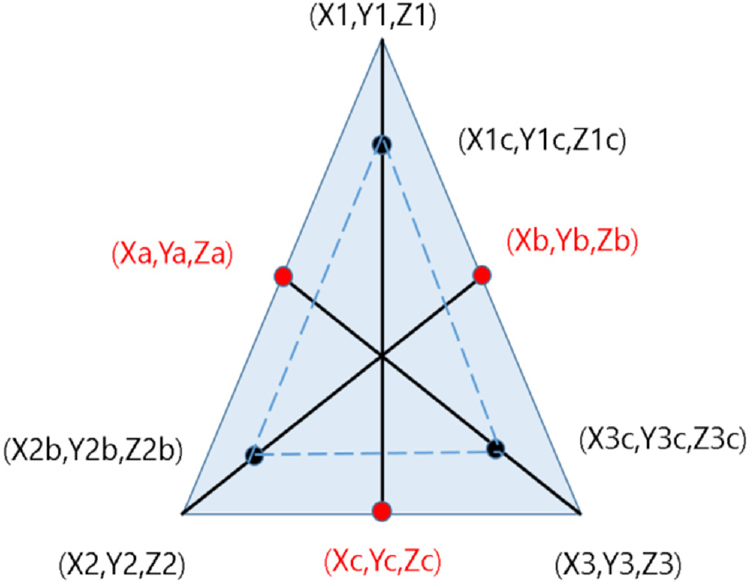
Calculation of the 1:(N-1) position of the line connecting each vertex with the corresponding side center
이어서, 가열경로 생성시에 가열방향 및 가열순서를 결정하기 쉽도록 하기 위하여 Fig. 9에 도시된 바와 같이, 각변의 등분점을 RM1과 RMe, BM(밑변) 등으로 구분한다. 여기서, M은 2,3,4,5, 등으로 순차증가한다.
이어 Fig. 8 과 같이, 밑변을 제외한 2개의 변에 생성된 등분점 RM1과 RMe를 잇는 선분의 N등분점을 계산한다. 여기서, N은 RM1과 RMe를 잇는 거리를 EL로 나눈 몫이다.
마지막으로, 계산된 각 RM1과 RMe의 등분점에 인덱스(index)를 부여하고, 상술한 계산 단계에서 생성된 등분점의 X,Y,Z 좌표값을 배열(array)을 이용하여 저장장치에 Fig. 9 와 같이 저장한다.
한편, 열원 중심이 이동할 좌표를 계산하는 단계에 이은 가열 순서를 결정하는 단계는 상기 저장장치(Fig. 9)에 저장된 좌표값을 배열 순서대로 (1,1) → (2,1) → (2,2) → (3,1) →로 가열 순서를 제공받으며, 가열 방향을 바꾸고자 하는 경우에는, 배열의 순서를 재배치하여 사용한다.
마지막으로, 열원의 회전가열 등을 설정하는 단계에서는 열원특성 DB로부터 제공된 정보에 따라 열원의 회전가열 등을 설정하는데, 여기서 상기단계에서 생성된 각 좌표의 위치는 열원 중심이 이동해야할 좌표에 해당하므로, 각 좌표에 열원이 이동하였을 때, 위빙(weaving) 효과를 구현하기 위하여 수행된다. Fig. 10 으로부터 알 수 있는 바와 같이, 회전속도 및 회전횟수에 따라 투입되는 열량 제어가 가능하게 되므로, 과다한 입열량에 의하여 강재의 표면에서 발생할 수 있는 용융(melting) 현상을 방지할 수 있게 된다. 열원의 이동 중심점을 기준으로 회전해야할 회전반경은 열원의 크기에 따라 그 크기를 다르게 할 수 있으며, 이 역시 열원특성 DB에 데이터베이스화하여 사용된다.
한편, 가열 효율측면에서도 열원 중심이 이동할 좌표 생성시에 열원의 중첩 가열효과를 구현하기 위하여 Fig. 11 에 도시된 바와 같은 열원 반경을 고려한 등분 방법을 선택하였다. 이는 회전 가열방법과 연결되어 수축변형이 충분히 발생할 수 있는 열량 투입을 가능하게 하여, 실제 작업자의 수작업에 의한 방법과 동일한 가열 효과를 구현할 수 있다.
4. 오목형 곡면 삼각가열 실험
구성된 자동화 장치 및 가공정보 생성 시스템을 활용하여 오목형 곡면의 열간가공 실험을 수행하였다.
실험에 사용된 곡면 부재는 Table 1과 같으며 오목형(concave) 곡면의 형상은 Fig. 12와 같다.
Fig. 13 은 초기 프레스 벤딩된 곡면의 형상을 계측장치를 통해서 계측을 수행 후 가공정보 생성시스템에서 1회째에 제시된 가열선의 형상(삼각가열 형상)을 나타낸다. 총 8개의 삼각 가열선이 제시되었다. Figs. 14, 15, 16, 17, 18 까지 그림은 2,3...6차 까지의 가공정보시스템에서 생성된 삼각가열선에 나타낸다.
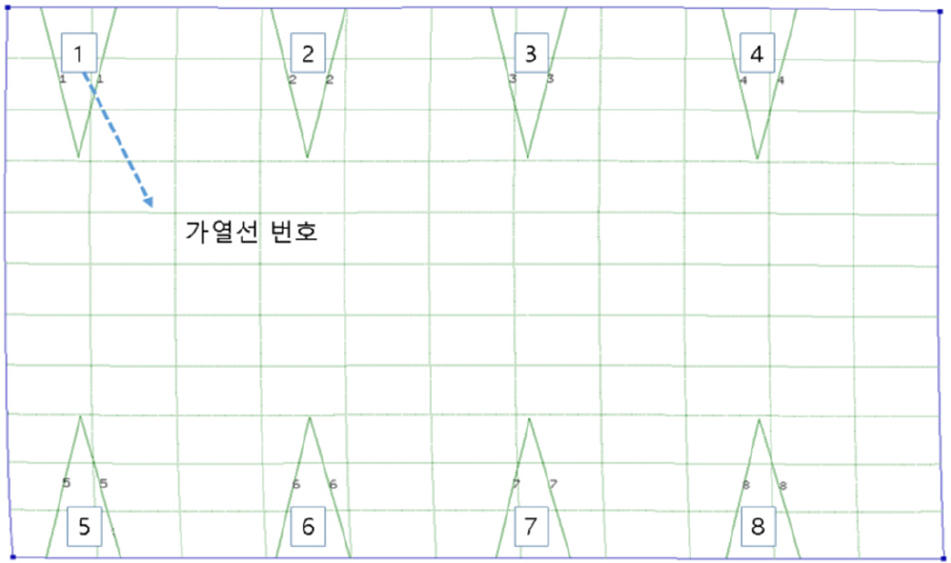
Triangular heat line generated from the initial cold bended plate(first generated triangular heat line)
Fig. 20 은 총 6차례의 반복 가열작업을 완료 한 이후에 최종형상에 대해서 목적형상(CAD surface) 와 계측 형상(measure surface)을 곡면 정합하여 그 오차를 나타낸 결과이다. 초기 형상은 최대 60mm 정도 오차가 발생하였으나(Fig. 19), 최종 형상은 최대 13mm 정도 오차가 발생하는 결과로 목적형상과 거의 유사함을 확인 할 수 있었다. 곡면형상은 Horn(1987)이 제안한 정합 알고리즘을 이용하여 정합을 수행하였다.
5. 결론
곡가공 자동화를 위하여 제안된 요소기술을 보완 적용하여 실제 조선소에서 사용 가능한 시스템을 제안하였으며, 오목형(concave) 곡면 성형 실험을 통하여 시스템의 타당성과 실용성을 검토하였다.
고주파 유도가열 열원을 이용한 삼각가열에 대한 가열패턴을 제안하여 그 실용성을 검증하였으며, 실제 오목형 곡면 테스트를 통합 가공정보 시스템과 자동화 가열 장치는 반복 가열 작업을 수행하였으며 최종형상은 목적곡면에 유사함을 확인 하였다.
References
-
Bae, K.R., Yang, Y.S., Hyun, C.M., Won, S.H., & Cho, S.H., 2007. Derivation of simplified formulas to predict deformations of plate in steel forming process with induction heating. Journal of Society of Welding and Joining of Korea, 25(4), pp.396-402.
[https://doi.org/10.5781/KWJS.2007.25.4.058]
-
Horn, B.K.P, 1987, Closed-form solution of absolute orientation using unit quaternions. Journal of Optical Society of America, 4(4), pp.624-629.
[https://doi.org/10.1364/JOSAA.4.000629]
- Jang, C.D., Ko, D.E., Kim, B.I., & Park, J.U., 2001a, An experimental study of characteristics of plate deformation by heating process. Journal of the Society of Naval Architects of Korea, 38(2), pp.62-70.
- Jang, C.D., Ko, D.E., Mun, S.C., & Seo, Y.R., 2001b, Simulation of plate deformation by triangle heating process. Journal of the Society of Naval Architects of Korea, 38(4), pp.66-74.
- Jang, C.D., Ha, Y.S., & Ko, D.E., 2003, An improved inherent strain analysis for the prediction of plate deformations induced by line heating considering phase transformation of steel, 13th International Offshore and Polar Engineering Conference, 4, pp.147-152.
- Kang, J.K., Lee, J.H., & Shin, J.G., 2000, Numerical analysis of induction heating for the application of line heating. Journal of the Society of Naval Architects of Korea, 37(3), pp.110-121.
- Kim, H.K., 2002, Simulation of line heating by high frequency induction heating, Ph. D. Seoul National University, Korea
- Kim, T.H., 2001, A study on the prediction of plate deformation by triangle heating using inherent strain method, M.S. Seoul National University, Korea.
- Kim, Y.B., 2007, A determination of heating shape and position for triangle heating, M.S. Seoul National University, Korea.
-
Kim, Y.B., Park, J.S., Shin, J.G., Hyun, C.M., Kim, D.K., & Ko, K.H., 2009, The determination of heating shapes and locations for triangle heating. Journal of Manufacturing Science and Engineering, 131(2), 021007, ASME, April.
[https://doi.org/10.1115/1.3090886]
- Ko, K.H, Park, J.S., & Shin, J.G., 2005, Towards automatic measurement and comparison of curved hull pieces in the line heating process, ICCAS2005, 19(1), pp.8-15.
- Park, J.S., Shin, J.G., Hyun, C.M., Doh, Y.C,. & Ko, K. H., 2007. Development of automated line heating information extract system for fabrication of curved hull plates. International Conference on Computer Applications in Shipbuilding, pp.159-168.
- Ryu, C. H., 2002, A consistent algorithm for unfolded flat shape of curved ship's hull shells by minimizing strain energy, Ph.D. Seoul National University, Korea.
- Seo, Y. R., 2000, A simulation of plate deformation by triangular heating process, M.S. Seoul National University, Korea.
- Shin. J.G, Ryu. C.H., Lee, J.H., & Kim, Y.D., 2003, A user-friendly, advanced line heating automation for accurate plate fabrication, Journal of Ship Production, 19(1), pp.8-15.
-
Terasaki, T., Mizukami, M., Nakatani, M. & Ohsawa, M., 2003, Effect of line heating factors on transverse shrinkage generated by triangle heating, Journal of the Society of Naval Architects of Japan, 193, pp.75-83.
[https://doi.org/10.2534/jjasnaoe1968.2003.193_75]
- Ueda. Y., Murakawa, H., Mohamed, R. A., Okumoto, Y. & Kamichika, R., 1994, Development of computer-aided process planning system for plate bending by line heating(report 2) - practice for plate bending in shipyard viewed from aspect of inherent strain, Journal of Ship Production, 10(4), pp.239-247.